During standard sewage sludge carbonization program, most of the carbon that is contained in the organic matter is eventually released into the air as carbon dioxide. This isn’t a huge problem since the carbon in most sewage sludge is regularly cycled from living plants and animals and back into CO2 over and over again. The problem with fossil fuels is that it’s coming out of the ground after 400 million years of being buried and upsetting the climate that way. However, if the huge amount of sewage sludge from every city in the US was to be converted to bio-char, that could turn into a massive carbon sink that could be churned back into the soil where it could last up to 1,000 years. It could also be used to make oil and gas to replace fossil fuels as well. Here is how that could be done using a sewage sludge carbonizing plant.
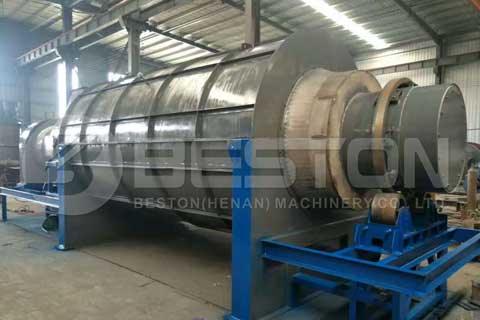
The Actual Process Isn’t New
For thousands of years ancient civilizations have been making charcoal from trees they’ve cut down. The process is simple, they cut and then pile up a huge amount of trees and brush, then cover the pile with wet leaves and on top, thick dirt.
Then, they light the wood inside and close off the oxygen to let the wood only partially burn because of the lack of oxygen. That’s how you make charcoal the old fashioned way. Of course, now we have new charcoal manufacturing plant that is far more efficient, but the basics are the same.
As It Turns Out, The Process Works On Most Organic Waste
This process has a name, pyrolysis, and that’s when you bake any organic material, whether it’s coconut shells, corn husks, or sewage sludge, until it breaks down into basic ingredients. That will also depend on how long you bake it and what components are in the material. The reason the baked organic material doesn’t burn is that oxygen has been eliminated from the equation. Without oxygen, nothing burns, no fumes are emitted, and no toxic chemicals are created. Therefore, this process is also the process of charcoal production.
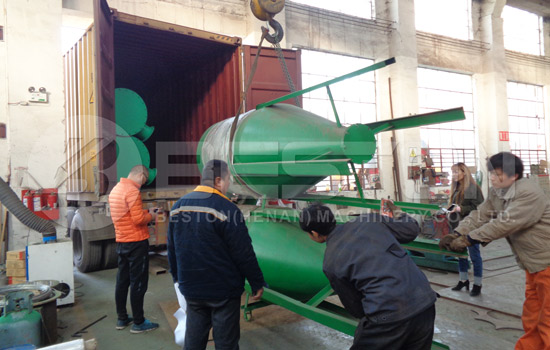
Lately the charcoal manufacturing plant has been being made to consume everything from waste tires, plastics, straw, restaurant waste, and olive pits, to now sewage sludge. There is a difference in the machines that are able to handle each different type of waste but the basic process is the same.
For Sewage Sludge Preheating Is Required
Sometimes the initial stage is called “dewatering” but what it entails is drying the sludge from about 75% water to about 35% water. Most pyrolysis plants that are made specifically for sludge will use the heat from the reaction chamber to preheat and dry the sludge. That helps keep costs down and the process running smoothly and fully self-contained.
The dried sludge is then fed onto a screw conveyor that will admit the sludge to the reactor chamber without oxygen. This is important to prevent combustion at the 600 C that the sludge will be baked at. The heated sludge will release combustible gases which are captured and used to heat the reactor, again, keeping the system self-contained and efficient.
Beston Machinery Henan will provide you more information about the pyrolysis and charcoal production during the process of sewage sludge carbonization program.